アプリケーションの放熱要件を満たすには設計時にさまざまな半導体パッケージの熱挙動を比較検討する必要があります。今回のNexperiaのブログでは設計者が最適なパッケージを選択できるよう、ワイヤーボンディングとクリップボンドのパッケージにおける放熱経路について解説します。
ワイヤーボンディング・デバイスにおける熱の流れ
ワイヤーボンディングのデバイスでは基準点の接合部からプリント回路基板(PCB)上のハンダ点までが主な熱の流れとなります(図1参照)。熱抵抗計算では一次近似として、副次的な電力損失経路(図1参照)の寄与は無視できます。
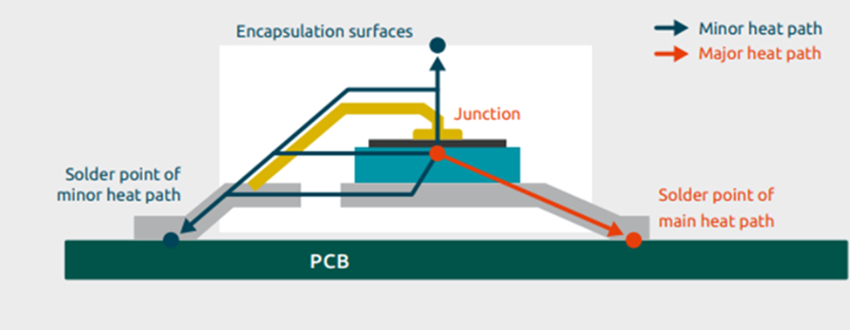
クリップボンド・デバイスにおける熱の2つの流れ
熱の観点で見ると、クリップボンド・パッケージはデバイスの接合部から放出される熱が、リードフレーム(ワイヤーボンディング・パッケージと同様)とクリップフレームの2経路を通過する点で、ワイヤーボンディングと異なります。
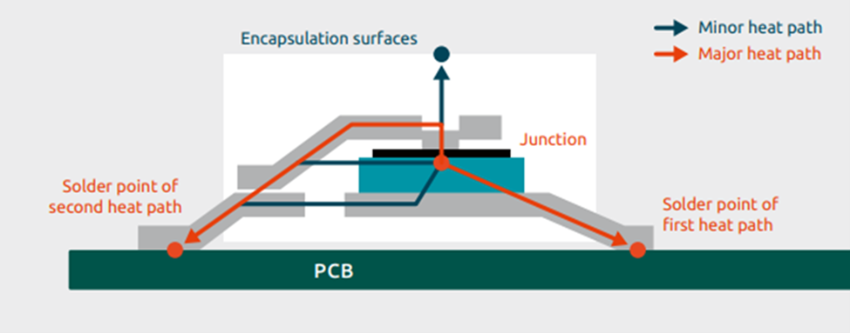
2か所に基準のハンダ点があるため、接合部からハンダ点までの熱抵抗Rth(j-sp)の定義が複雑になります。温度も異なる場合があるので、熱抵抗は並列ネットワークになります。
Nexperiaでは、クリップボンドとワイヤーボンディングの両デバイスにおいて、同じ方法でRth(j-sp)の値を抽出しています。この値はダイからリードフレーム、そしてハンダ点に至る主要な放熱経路の特徴を表すもので、この値でクリップボンド・デバイスと同種のPCBレイアウトのワイヤーボンディング・デバイスを比較することができます。ただし、Rth(j-sp)の値を求める際に第2経路全体を使用しないため、デバイス全体の放熱能力は高めになる傾向があります
第2の主要放熱経路があるということはPCB設計を改善するチャンスがあるということでもあります。例えば、ワイヤーボンディング・デバイスでは放熱が可能な経路は1つ(ダイオードの放熱は一般的にカソード端子を経由する)しかありませんが、クリップボンド・デバイスでは2つの端子を使用することができます。
半導体デバイスの熱特性シミュレーション
シミュレーションでは、PCB上におけるすべてのデバイス端子に放熱経路を設けることで熱特性が大幅に向上することが確認できます。CFP5パッケージ(図3)のPMEG6030ELPダイオードの熱は35%が銅クリップからアノードピンに放出され、残りの65%がリードフレームを介してカソードピンに放出されています。
図3:CFP5パッケージのダイオード
また、シミュレーションでは図4のようにヒートシンクを両端子に分割することが、放熱に有利であることを示しています。両端子に0.5cm2のヒートシンクを配置すると、カソードのみに1cm2のヒートシンクを配置した標準設計に比べて、同じ温度で約6%多くの電力を放散できることも分かります。3cm²のヒートシンクを両端子に使用すると、標準的な設計でカソードのみに6cm²のヒートシンクを使用した場合よりも、約20%放熱電力が増加します。
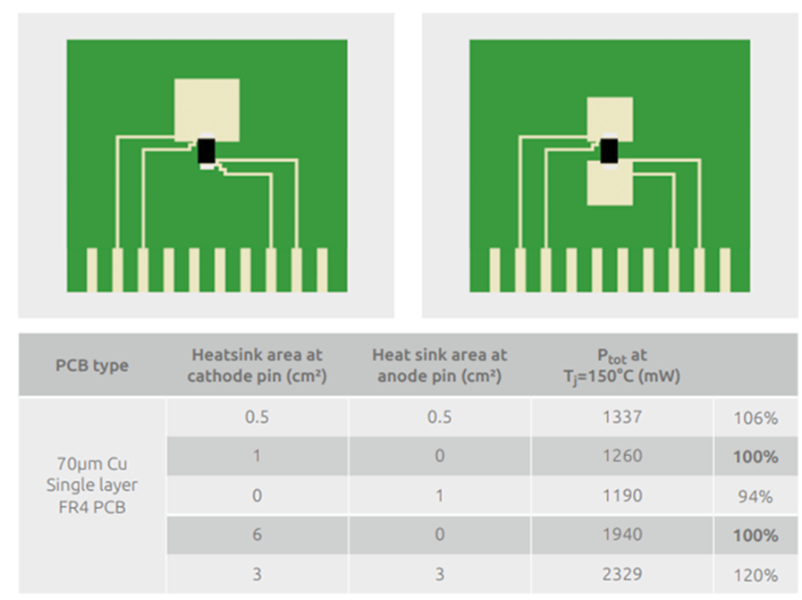
アプリケーションに最適なパッケージ選択をNexperiaがサポート
"半導体デバイスメーカーによっては、設計者がアプリケーションに最適な熱特性のパッケージを選ぶ際に必要な情報を提供していない場合があります。
今回のNexperiaの記事では、設計者がアプリケーションに最適な選択ができるよう、ワイヤーボンディングとクリップボンドのデバイスにおける放熱経路について解説しました。
詳細についてはNexperiaの『Diode Application Handbook(ダイオード・アプリケーション・ハンドブック)』をご覧ください。"
設計の際にダイオードとトランジスタ用に省スペースの熱を最適化した堅牢なパッケージをお探しならば、次のランディング・ページをご利用ください: nexperia.com/save-pcb-space