过去,简单的12 V铅酸电池是几乎所有汽车的普遍配置,这意味着保护车辆电气设备免受静电放电(ESD)是一项相对简单的任务。然而,汽车结构正在发生根本性的快速变化,这意味着设计人员现在需要更广泛的ESD保护器件选择,以确保车辆在道路上安全运行。这篇博客文章探讨了导致汽车电力系统供电所用板网电压变化的一些因素,并讨论了Nexperia符合AEC-Q101标准的全新ESD保护器件产品组合的特性,其中包括灵活的选项,可保护采用12 V、24 V和48 V板网运行的电路板。
为何板网电压不断升高
汽车中的电气和电子元件数量不断增加,其所需的电量现已达到12 V电池系统的极限。合理的解决方法是增加电池电压,为了适应这种变化,汽车公司已经开发出可以从24 V(现在通常用于重型商用车)到48 V运行的电气系统,并且被越来越多的新型混合动力电动汽车(HEV)采用。电池电压不断升高的趋势意味着传统的铅酸电池最终可能会被锂离子电池取代。与12 V电池相比,48 V系统的功率输出和效率显著提高。更高电压的另一个优点是,在输出相同功率的情况下,可以降低电流水平,这意味着可以使用更细、更轻的电缆,这对电动汽车来说是一个重要的要求。因此,对于需要消耗大量电流的动力设备(如泵、压缩机和悬架组件),更合适较高的电压。配备48 V电池的车辆仍采用12 V系统来为电子控制单元(ECU)以及CAN和LIN等传统汽车网络接口供电。然而,这些系统的12 V电源是通过使用降压转换器降低48 V电池电压来产生的。图1显示了用于描述各种电路板网电压的条件。
保护12 V CAN系统
控制器局域网(CAN)是一种值得信赖的传统汽车通信协议,通常使用双线双绞线电缆来传输和接收串行数据(图2)。CAN收发器在网络中的协议控制器和物理总线线路之间提供物理链路。高速CAN指定传输速率高达1 Mbit/s,而低速容错CAN指定数据速率高达500 kbit/s。CANL是指低电平CAN总线,CANH是指高电平CAN总线。在正常工作模式下,显性态的值约为1.4 V,隐性态的值为5 V。在低功耗模式下,CANL的电压与电池电压相同(通常为12 V),但在正常工作模式下,显性态电压约为3.6 V,隐性态为0 V。为了防止ESD并确保仍能进行通信,可以在CANH和CANL线路上应用外部钳位电路。Nexperia提供经过专门设计的ESD保护器件,以保护两条CAN总线线路免受ESD及其他瞬变现象造成的损坏。由于CAN网络可短路接至电压源,例如汽车电池,因此CANL和CANH线路上的ESD保护器件必须能够耐受更高电压电平。为了安全承受跨接启动条件或商用车中两个12 V电池串联的情况,Nexperia的ESD保护器件满足24 V的最低要求截止电压(VRWM),并遵守ISO7637-2和ISO 16750-2 ESD保护标准。
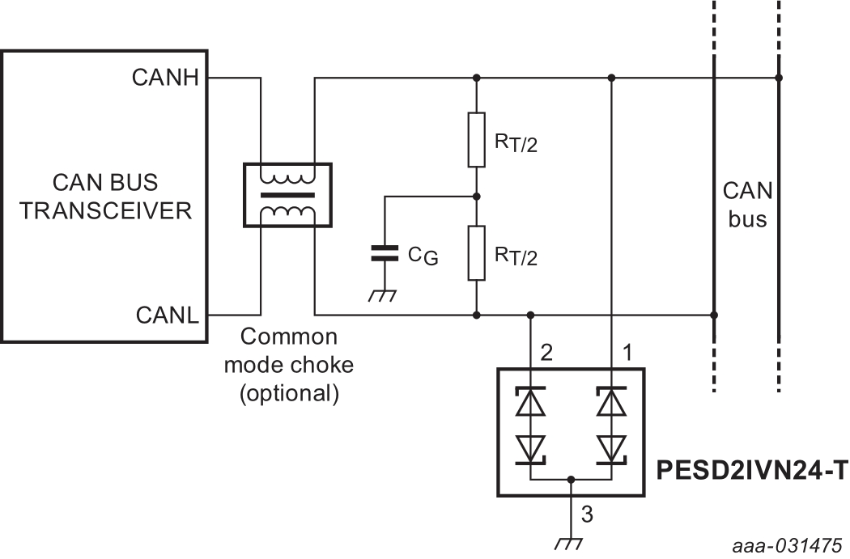
保护24 V和48 V系统
汽车和小型车辆通常使用12 V电池电压,而24 V板网通常用于卡车和商用车辆。根据ISO7637-2和ISO 16750-2 ESD保护标准,需要使用工作电压通常高于32 V的ESD保护器件来保护24 V板网中的敏感信号线。Nexperia将新产品组合中的器件设计为最大反向截止电压为36 V,并提供高达22 kV的ESD保护。该性能加上IPP = 1 A时的48 V低钳位电压VCL,为车载网络提供了出色的系统级稳健性。Nexperia还为48 V网络提供ESD保护器件,该设备满足ISO 21780中定义的附加要求。
Nexperia的ESD保护器件可最大程度地提高设计灵活性
为了实现最大的灵活性,该产品组合中的所有器件(12/24/48 V)均采用SOT23和SOT323封装,具有4 pF、6 pF和10 pF三种不同的电容等级,有助于确保接口之间的顺畅通信,而不会影响信号完整性。这种组合最大限度地提高了PCB设计的灵活性,并为设计工程师提供了多种性能选项。Nexperia全系列汽车ESD保护器件的规格如下表1所示。