功率密度在汽车系统中举足轻重。无论是传统的电子转向和制动系统,还是新型48V/12V混合动力和全电动汽车(EV)系统,都是如此。Nexperia的最新LFPAK88铜夹封装将小尺寸、低导通电阻、高ID的优点集于一身,实现了1 W/mm3以上的功率密度。
作为各个市场大量应用的主要动因,功率密度在汽车系统中举足轻重。例如,在电动助力转向中,我们正在向双重冗余迁移,旨在提高系统安全性,这使电子元件数量增加一倍,但需要占用的空间不会同等增加。
随着更多48伏特轻度混合动力汽车投入生产,我们也看到更多汽车应用的引入,例如皮带传动起动发电机(BSG)和12/48V DC/DC转换器,帮助降低二氧化碳排放量。这些模块同样受到当前的空间限制,因而我们需要高功率密度的解决方案
在所有这些情况下,LFPAK88都能真正提供帮助。它将小尺寸、低导通电阻、高ID的优点集于一身,并且可以达到1 W/mm3以上的功率密度 – 在每立方毫米的体积内提供很高的功率!首先,我们通过直观的比较,展示该封装相对于其他封装的改进。下表显示了使用相同汽车级40 V超结技术平台的多款产品,用以展示封装而非芯片带来的变化。对于LFPAK88,这些包括先前最低的0.7 mΩ导通电阻器件和新发布的0.55 mΩ器件。
器件编号 |
封装 |
ID最大值(A) |
导通电阻(mΩ) |
功率密度(W/mm³) |
LFPAK88 |
425 |
0.7 |
1.16 |
|
BUK761R2-40H |
D²PAK |
120 |
1.2 |
0.02 |
正如上表中所示,我们不仅能够进一步降低导通电阻,还能够显著增加漏极电流最大值。考虑到节省空间方面,与3引脚的D²PAK相比,Nexperia的LFPAK88现在将汽车BUK7S0R5-40H和工业PSMNR55-SSH的功率密度提高了53倍(对比先前的48倍)。值得注意的是,由于LFPAK88具备明显的优势,D²PAK BUK761R2-40H经开发后并未发布。
这种高功率密度是如何实现的?总体而言,它是通过创新的封装技术和改进的芯片技术实现的。就LFPAK88封装本身而言,有三个因素与提高功率密度相关:
- 更高的电流能力可以增加功率
- 更小的封装外形可以提高密度
- 更高的效率可以减少散热问题。
下面我们简单地依次讨论这三大因素。
夹片与线缆 – 优于当前的连接
在D²PAK及其不同版本中,芯片与封装引出端之间采用线缆连接,这就限制了它能够处理的电流量。LFPAK使用的铜夹片技术在芯片和引出端之间提供更大面积的接触,从而能够处理更大的电流,提高输出功率。
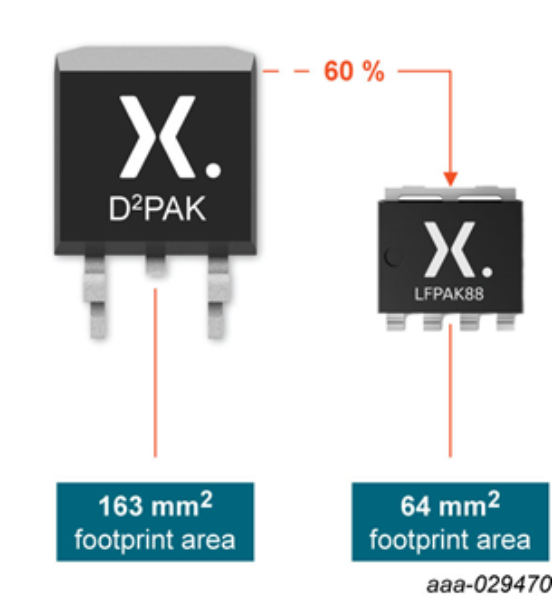
缩小外形体积
在选择LFPAK88封装外形时,我们在封装电流、散热能力、占位面积三者之间达到了最佳折衷,使其适合更高功率的应用。外形体积为8.0 x 8.0 x 1.6 mm,在长度、宽度和高度方面均小于前一代的D²PAK和D²PAK-7,与D2PAK相比,占位面积减小了60%,整体占用空间减少了86%。
高效易散热
在更小的面积内操作更高的电流,效率至关重要,效率提高便无需处理多余的热量。高效率意味着有更多功率被用于执行任务。LFPAK通过减小导通电阻来实现高效率,因为铜夹不会增加电阻,这一点与内部焊线有所差异。没有焊线连接到源极,再加上外部源极引脚很小,这也会减小寄生源极电感。在今后的博客中,我将更详细地讨论寄生源极电感和热效率。
芯片支持
更新的芯片技术还有助于提高功率密度。Nexperia采用了汽车级超结技术,单元间距更窄,因而减小了封装导通电阻。这样可以达到更高的效率,提高IDmax性能。
最新动态…
提高功率密度仍然是产品设计中一个至关重要的因素。为此,新的铜夹LFPAK88封装与超结芯片技术相结合,提供了出色的功率密度性能。在初始版本中,Nexperia推出了能够处理425 A的0.7 mΩ @ 40 V器件(BUK7S0R7-40H)。现在新发布的0.55 mΩ器件(BUK7S0R5-40H 和 PSMNR55-40SSH)已测得电流能力可达500 A。
0.55 mΩ新器件的发布不仅带来了更优秀的的功率密度,而且还开启了汽车内的新应用。从现有电池保护器件到出于可靠性原因而更换的新保险丝和继电器,对此类低导通电阻器件的需求变得日益重要。